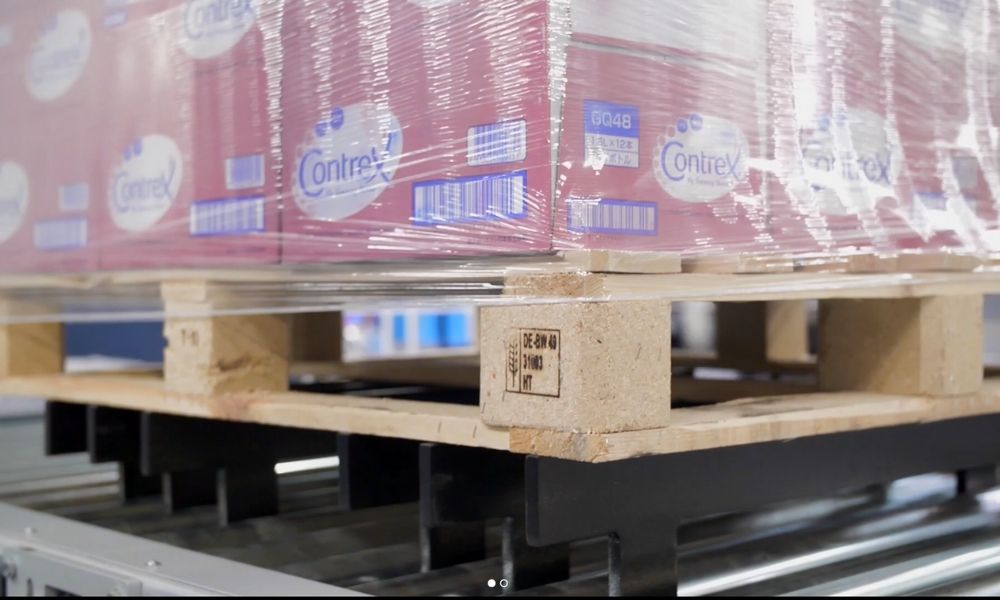
Heat shrink tube, an often-underestimated component in various industries, is a genuine technological marvel. The versatile roles it plays – from providing insulation and protection to offering strain relief and aesthetic enhancements – often go unrecognized. So, this article aims to demystify the captivating technology behind heat shrink tubing, elucidating its importance in numerous modern-day applications.
Unraveling the Fundamentals
At its core, a heat shrink tube, often simply referred to as heat shrink, is a specially formulated plastic tubing that contracts or shrinks in diameter when exposed to heat. This transformative process is made possible due to the unique properties of thermoplastic materials used in its production, such as polyolefin, fluoropolymer, PVC, neoprene, and silicone elastomer. These materials are specifically chosen for their ability to provide secure, insulative, and flexible coverings for various electrical components, including wires, terminals, and joints, among others.
How Does Heat Shrink Work?
The underlying science of heat shrink tubes is fascinating. The key process it undergoes is known as radiation cross-linking. Here, the thermoplastic material is exposed to high-energy radiation, forming cross-links among the polymer chains. When the tubing is heated later, it attempts to revert to its original, pre-expanded diameter. However, the cross-links formed earlier prevent a full reversion, leading to a tightly conformed, protective seal around the encapsulated component.
The Benefits of Heat Shrink
The advantages offered by heat shrink wrap are wide-ranging and substantial. Primarily known for its excellent insulation and protection capabilities, it acts as a defensive shield against electrical shorts and safeguards against harsh environmental factors like moisture, chemicals, and physical abrasion. Adding to its protective qualities, it mitigates stress on cables and connections through its strain-relief capability. From an organizational standpoint, color-coded heat shrink wrap aids in easy wire identification, enhancing the aesthetics of the wiring setup.
Common Applications of Heat Shrink Tubing
The diverse application spectrum of the tubing is a testament to its versatility. Electronics extensively use it for wire bundling and insulation purposes. The automotive industry appreciates its protective prowess for cable harnessing, and the aerospace sector values its lightweight and reliable insulation. Remarkably, it is making strides in the medical field as well, providing biocompatible insulation for medical devices.
Choosing the Right Heat Shrink Tube
Choosing the appropriate heat shrink wrap is calculated and hinges on various factors. These include the nature of the application, environmental conditions, and the dimensional requirements of the component. Materials used in the tubing determine its flexibility, chemical resistance, and heat tolerance. Additionally, the shrink ratio, which is the extent of size reduction when heated, is critical in determining its suitability for different applications.
Heat Shrink Tube Installation
The installation process of the tubing involves sliding the tubing over the component and applying heat uniformly around it. This process can be performed using several tools, such as heat guns, ovens, or infrared heaters. Meanwhile, adequate care must be taken to prevent overheating, as it can compromise both the integrity of the tubing and the underlying component.
Innovation in Heat Shrink Tube
Innovation is shaping the future of heat shrink tubes, driving advancements in materials, designs, and manufacturing processes. The industry is continuously evolving, with tubing offering higher shrink ratios, enhanced environmental resistance, and specialized properties like flame retardance and low smoke generation. These advancements are expanding the potential applications of this versatile technology.
Heat shrink tubing, with its unique properties and diverse applications, is an unsung hero in the technological world. As you demystify the technology behind it, you appreciate its contribution to safe and efficient electrical and mechanical systems. As such, understanding the workings of heat shrink wrap is a step towards better harnessing its potential and enhancing safety, performance, and aesthetics in various applications. From the automotive industry to medical devices, the reach of heat shrink tubes is expansive, making it a technological marvel worth understanding.