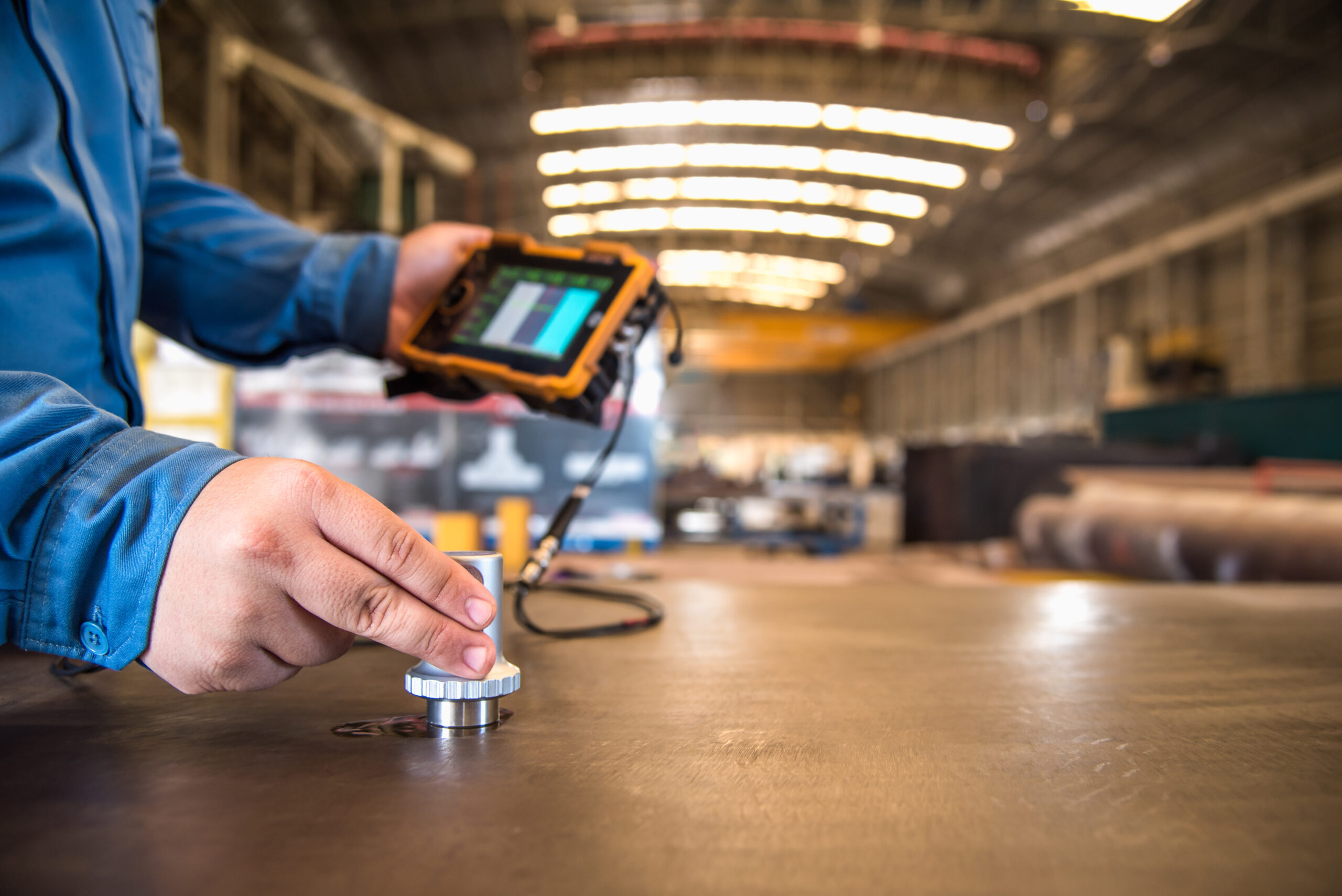
Ensuring the safety and quality of structures and products in various industries is crucial for the well-being of both humans and the environment. One of the most important methods used for this purpose is evaluating the properties of a material, component, or system without causing any damage to it. This technique, known as non-destructive testing (NDT), has become an essential aspect of quality control and safety management in a wide range of fields, such as aerospace, automotive, construction, and manufacturing. These techniques range from simple visual inspections to sophisticated imaging methods such as X-rays and ultrasounds.
To find out more about why NDT matters in ensuring safety and quality, read the section below.
The Benefits of NDT
One of the primary benefits of non-destructive testing is that it allows inspections to be conducted without dismantling or destroying the tested materials. This reduces costs and minimizes the risk of damaging the item being tested. For example, in the aerospace industry, NDT inspects aircraft components, such as wings and engines, which can’t be removed without causing damage. By using NDT, inspectors can detect cracks, corrosion, and other defects that could compromise safety without dismantling the component.
NDT can also detect defects that are not visible to the naked eye. For example, ultrasonic testing uses high-frequency sound waves to detect internal flaws in materials such as welds, castings, and composites. These flaws can include cracks, porosity, and inclusions, which could weaken the material and lead to failure under stress. By detecting these defects early, NDT can help prevent catastrophic failures and ensure the reliability and safety of critical components.
The Versatility of NDT
NDT is highly versatile and can inspect various materials and structures. For example, radiographic testing can be used to inspect welds, castings, and forgings in metals. In contrast, eddy current testing can examine conductive materials such as aluminum and copper. In addition, NDT can be used to inspect concrete structures such as bridges and buildings and composite materials used in aerospace and automotive applications.
The Importance of Choosing the Right NDT Technique
It’s important to note that NDT is not a one-size-fits-all solution. The choice of technique will depend on the material being tested, the type of defect being looked for, and the desired level of accuracy. For example, radiographic testing may not be suitable for inspecting thin or low-density materials, while eddy current testing may not be effective for detecting subsurface defects. Choosing the appropriate NDT technique requires a thorough understanding of the material being inspected and the specific defect being looked for.
The Importance of Skilled Technicians in NDT
NDT requires highly trained and skilled technicians to perform the inspections and interpret the results. Technicians must be familiar with the specific NDT technique, the material being inspected, and the type of defect being looked for. They must also be able to accurately interpret the results and determine whether any defects found are critical or non-critical. This requires a high level of expertise and experience in the field of NDT.
Non-destructive testing is critical in ensuring safety and quality in many industries. By allowing for inspections to be conducted without causing damage, detecting defects that are not visible to the naked eye, and being highly versatile, NDT can help prevent catastrophic failures and ensure the reliability of critical components. However, it’s important to remember that NDT is not a one-size-fits-all solution and requires highly trained and skilled technicians to perform the inspections and interpret the results. By using NDT appropriately and relying on the expertise of trained professionals, industries can ensure the safety and quality of their equipment and materials.