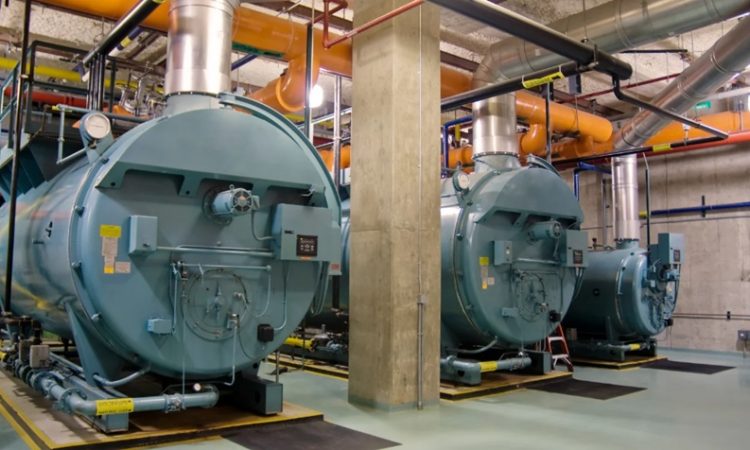
Water plays a central role in the operation of any industrial boiler system. When water quality is compromised, so is performance, efficiency, and safety. Industrial boilers are highly sensitive to contaminants like minerals, gases, and organic compounds, all of which can impact energy use and system lifespan. For any setup for an industrial boiler in Oklahoma, where water conditions vary significantly, proactive water treatment becomes even more important. Even the most advanced equipment can fall short without consistent attention to water purity.
Let’s take a closer look at how water quality influences boiler systems and why professional oversight is essential.
The Role of Water in Boiler Operation
Water circulates through boilers, transferring heat and generating steam that powers equipment or maintains temperature control. But this process is only as efficient as the water’s composition allows. Impurities in water can lead to buildup, corrosion, and thermal stress.
In many industrial settings, the performance of boiler components like valves, burners, and pumps depends heavily on consistent conditions throughout the system. These interactions reflect the complexity of boiler design, especially where mechanical balance and thermal regulation must work in sync—similar to the way boiler systems operate across various commercial environments under changing load demands.
Common Water Quality Issues That Affect Boiler Performance
Water used in industrial boilers can introduce a range of problems if left untreated. The following issues are among the most common:
1. Scale Buildup from Hard Water
Hard water, which contains calcium and magnesium, causes scaling on internal surfaces. This mineral buildup acts like insulation, reducing heat transfer efficiency and forcing the boiler to consume more fuel to maintain output.
2. Corrosion Due to Oxygen and Acidity
When oxygen and acidic substances are present, they attack the metal surfaces inside the boiler. Corrosion weakens the structure, creates leaks, and increases the risk of equipment failure over time.
3. Foaming and Carryover
Impurities such as oils and organic material may create foam, leading to water droplets traveling with the steam. This carryover can damage downstream equipment, reducing overall system reliability.
4. Sludge Formation
Suspended solids and biological matter settle at the bottom of the boiler, forming sludge. This sludge reduces heating efficiency, clogs lines, and increases wear on mechanical parts.
Long-Term Impacts of Poor Water Quality
Neglecting water quality leads to more than just inefficiency—it can degrade the entire system. Consequences include:
- Elevated fuel consumption
- Increased frequency of service interruptions
- Costly component replacements
- Shortened equipment lifespan
Boiler systems that operate under stress from contaminants require more frequent maintenance and experience more unplanned downtime.
Why Professional Maintenance Matters
To keep boiler systems running at peak performance, water treatment must be handled by professionals. They evaluate water chemistry, manage dosing systems, and monitor conditions to prevent future issues. This hands-on approach is far more effective than reactive maintenance or system resets.
In large commercial operations, these systems are often integrated with broader HVAC infrastructure. That’s why industrial boilers are crucial to efficient HVAC performance in large buildings, where even minor inefficiencies in water quality can ripple through the entire system.
Conclusion
Water quality is one of the most critical factors in determining the performance and longevity of an industrial boiler. Scale, corrosion, foaming, and sludge can all be avoided through professional water treatment programs and regular system evaluations. For any facility using an industrial boiler in Oklahoma, the key to sustainable, efficient operation lies in expert care tailored to the system’s demands. Prioritizing high-quality water management protects your equipment—and your bottom line.